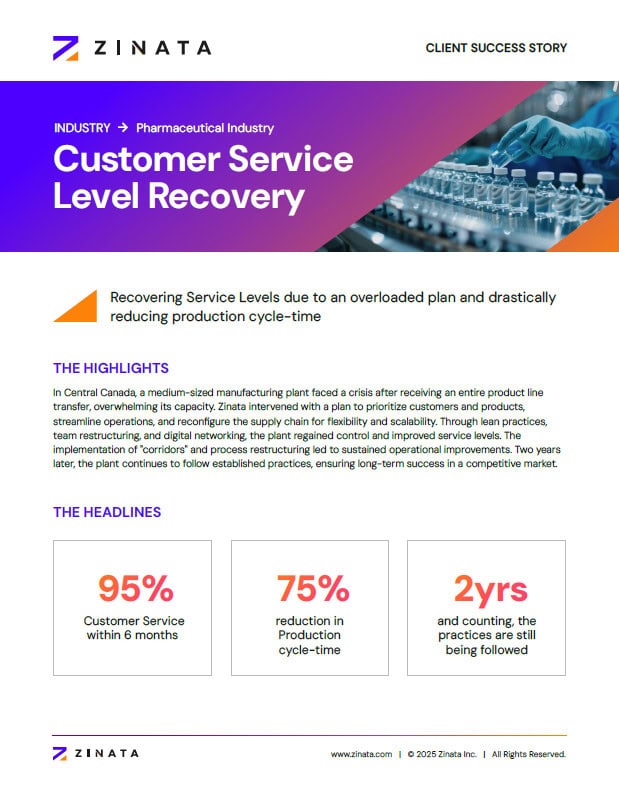
Download A PDF Copy Of This Case Study Here!
Customer Service Level Recovery
The Highlights
In Central Canada, a medium-sized manufacturing plant faced a crisis after receiving an entire product line transfer, overwhelming its capacity. Zinata intervened with a plan to prioritize customers and products, streamline operations, and reconfigure the supply chain for flexibility and scalability. Through lean practices, team restructuring, and digital networking, the plant regained control and improved service levels. The implementation of “corridors” and process restructuring led to sustained operational improvements. Two years later, the plant continues to follow established practices, ensuring long-term success in a competitive market.
The Headlines
- 95%: Customer Service within 6 months
- 75%: Reduction in Production cycle-time
- 2 Years: And counting. The practices are still being followed
The Challenge
A medium-sized manufacturing plant in Central Canada faced overwhelming volume after receiving an entire product line transfer, leading to a severe backorder crisis and loss of control.
- Customer Service levels below 65%.
- Quality holds exceeded 50%.
- Back orders were growing, customers were leaving, and the growing crisis was paralyzing operations.
- Excessive supply chain cycle time (7 months) and production cycle time (4 months).
- Raw material shortages frequently impacted schedules resulting in orders being missed.
Our Solution
Prioritizing customers and products based on business priority and value was the first step to stop the bleeding. Future-proofing operations involved reconfiguring supply chain and plant operations to be more flexible and scalable. Lean supply chain and operations management practices were implemented to streamline processes and reduce waste. The entire team was restructured to eliminate silos and integrate work, and end-to-end processes and systems were restructured for continuous flow planning and operation. Digital social networking facilitated collaboration across operational groups, and “corridors” with similar products were created.
Results & Impact
Zinata’s intervention in the Central Canada manufacturing plant exemplifies how strategic prioritization, lean practices, and team restructuring can turn around a crisis. By focusing on customer and product priorities and reconfiguring operations for flexibility, the plant not only recovered service levels but also significantly reduced production cycle times. The sustained success of these initiatives, even two years later, highlights the effectiveness of the implemented changes. This case demonstrates the power of comprehensive operational restructuring in achieving long-term success in the competitive pharmaceutical industry.
- Customer Service >95% in 6 months.
- Production cycle time reduced from 120 days to 25-30 days.
- Social networking applied to create a more cohesive operation.
- 2 years later the established practices are still being followed.